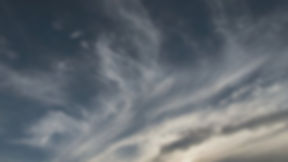
.png)
Piezo Accelerometer Tutorial
Accelerometer Properties
Accelerometer Properties
In this chapter we want to look at the main properties or typical characteristics of an accelerometer. Besides the definition, we want to examine and understand the influence of the construction on the properties of the vibration sensor.
There are also industrial standards treating the properties of a piezoelectric accelerometer. First to mention is the ISO 16063 standard about methods for the calibration of vibration transducers and the two older standards ISA-RP37.2-1982 (R1995) and ANSI/ASA S2.2-1959 (R2016) also describing the way of measuring certain characteristics.
To bring some order into the sea of properties, I have grouped them along three main axes, namely amplitude-related properties, frequency-related properties and finally temperature-related properties.
I have also tried to separate the “good” properties or design typical characteristics of a piezoelectric accelerometer from the “bad” ones, which I have named Disturbing Factors and are described in the last chapter.
Amplitude related Properties
In this section we find characteristics such as the sensitivity, the linearity, the dynamic range limited by the resolution and the permissible excitation as well as shock capability.
Sensitivity
The most concise characteristic of an accelerometer is probably the sensitivity which tells us how many pico-Coulombs are put out per unit acceleration.
In general the sensitivity S of a sensor is defined as the slope of the transfer function of that sensor. That means the ratio between the output change w.r.t. the related input change.
So the sensitivity S for the accelerometer becomes
S = dQ/da or S = ΔQ/Δa
Q = output charge [Q ] = pC (pico-Coulomb)
a = input acceleration [a ] = m/s² or g

The sensitivity corresponds to the slope of the curve Output vs Input
Some manufacturers of vibration sensors use pC/m/s² units for the sensitivity which is the correct dimension in the SI-system and also proposed by the ISO 16063 standard . However in wide parts of the industry particularly in aeronautics the base unit for acceleration is still the gravity g. This leads to the unit pC/g for the sensitivity.
Note: For a sensor which measures a static parameter (like temperature or pressure) we would talk about the static transfer function. However we remember hat the piezoelectric accelerometer cannot measure static acceleration. With our vibration sensor the (input and output) signal is always dynamic. Ideally the transfer function should be defined for a single distinct reference frequency. However as we will see under “Linearity” this might lead to some difficulties in testing the full transfer function.
Accelerometer Calibration (Reference Sensitivity)

The accelerometer calibration (measurement of the reference sensitivity) is established under a set of defined conditions. If you follow the ISO 16063 standard you could choose for example 50 m/s² at 160Hz.
Another traditionally established reference condition would be 5 g at 120 Hz or at 100 Hz
In practice the sensor calibration is determined by just one measurement of the output Q at the reference point, let’s say 5g at 120Hz.
Knowing that the transfer function is inevitably going through “zero”, the reference sensitivity is then simply S=Q/5 ; [S] = pC/g

120 Hz is used to avoid the first Harmonic of the 50Hz mains frequency.
For countries where the mains frequency is 60Hz the preferred reference frequency would be 100 Hz
The reference sensitivity will be the value to which all other measurements of performance characteristics or external influences will be referred to.
Calculation of the sensitivity (pro memoria)
To calculate the sensitivity of an accelerometer in pC/g we use the simple equation
S = m·d·g = m·d·9.81 ; [S] = pC/g
Where d is the resulting piezoelectric constant of the combined sensing element and m is the mass of the inertial mass of the accelerometer.
(most often d=n·dik with n = number of piezo elements)
From the above it follows that to increase the sensitivity of the accelerometer we need a piezo material with a high piezoelectric constant (dik ), a large number of piezo elements and a big inertial mass.
Measuring Setup
There are several methods for the accelerometer calibration (see also ISO 16063) but for all the measurements we need a shaker to produce a sinusoidal single axis motion. It is very important that the motion of the shaker is a close as possible in one single axis that means any cross axis movement must be minimised.
A typical measurement setup for the calibration (reference sensitivity) is a back-to-back mounting with a central block on which we mount the unit under test (UUT) on one side and a calibrated reference transducer on the other side. The whole assembly is mounted on a shaker. Both sensors must be mounted in the same axis to reduce the influence of any rocking motion of the shaker table.
A laser-based measuring device can also be used instead of the reference accelerometer, but it must also be aligned in the central axis.
There are dedicated back-to-back calibration sensors on which the UUT is mounted directly. Thereby the central mounting block can be omitted, however if the UUT have different mounting patterns a different calibration sensor is needed for each pattern.

Unit under
test (UUT)
Reference
Accelerometer
Shaker Input
Linearity
The transfer function of a sensor is ideally an straight line but in reality there are always small deviations from the ideal line. The linearity characterizes this ability of a sensor. According to ISA 37.1 Linearity is defined as: The closeness of a calibration curve to a specified straight line.
The linearity is expressed as non-linearity or linearity error. It is a measure of the maximum deviation of the accelerometer output from a specified straight reference line and is expressed as a percentage of the full scale (FS) output signal. In a few cases it is also specified as “percent of point”.

The linearity error is the deviation from the best straight line
Normally the reference is the “best straight line”, which is the straight line through all the measuring points that leads to the smallest offsets of all the points from the line.
It may also be defined in different ways for example the least error squares.
The linearity is often indicated with different values over different ranges. A typical indication would be 0.3% over 100g and 1% over 500 g
A piezoelectric element is considered one of the most linear means of converting a force into an electrical signal. Just make sure there is no mechanical shunt between the inertial mass and the base that could destroy the good linearity!
Measuring Setup
The linearity test is performed like the sensitivity calibration by comparison with a standard accelerometer. However with the calibration set-up as described above the amplitude capability or the power of the shaker may probably come soon to it’s limits. Therefore we use resonant structures like a transversely resonant beam or a longitudinally resonant rod to obtain the desired acceleration. The frequency of the resonant structure is normally higher than the one we have chosen for the calibration test. This is an accepable practice but the test frequency must remain in the lower end of the frequency band of the accelerometer under test because at higher ferquencies the output of the UUT might be inflenced by it's resonance.
On the resonant structure (the beam or rod) it is important to mount both the reference accelerometer and the UUT in close proximity and at a location far from the node point. It is also important that the ratio of the two outputs is measured throughout the complete range of accelerations on the same set-up.
Of course, a laser vibration meter can also be used as reference sensor.
Dynamic Range
The dynamic range of a sensor or instrument is defined as the range between the largest input versus the smallest input where the sensor remains within specification. A typical parameter to consider in this context is the linearity of the accelerometer.
The upper limit of the dynamic range is dictated by the architecture and design details of the accelerometer. It is given by the maximum allowable load, before it suffers from any permanent damage or before the signals gets unacceptably distorted or non-linear.
The lower limit is rather dictated by the signal resolution.
Maximum Load
The upper limit of the dynamic range is ultimately related to the weight of the inertial mass and the robustness of the piezo element. The larger the mass, the smaller the allowable acceleration. But not only the weight of the mass is important, but also the magnitude of the preload that holds the individual parts together. At the highest acceleration in all directions, the preload must be sufficient to prevent the parts from being shifted due to the inertial forces.
Resolution
The low limit of the dynamic range is generally determined by the resolution of the measuring chain. The resolution is defined as the smallest change in the input that still produces a change in the output. The resolution of a good accelerometer may be considered almost infinitely low. However in reality the resolution is determined by the measuring system noise. The system noise is largely determined by the electronics, cable length, cable screening , level of electro-magnetic environment, but also by triboelectric noise generated by cable motion or undesired base strain effects.
As a rule of thumb, a professional measuring system can clearly detect 1/100 of a pico-Coulomb with a signal-to-noise ratio that is still reasonable .
The lower limit of the dynamic range is determined by the electrical qualities of the measuring system while the upper limit is depending from the mechanical qualities of the accelerometer. Typically, a good piezo electric accelerometer operates over a dynamic range of up to 1’000’000 to 1 (120 dB).
Looking at the complete measuring chain we have to take into account that the subsequent electronics stages also have a maximum range limit above which we will get saturation clipping. I would like to point out that it is usually necessary to reduce the amplification at the resonance using a low-pass filter.
Shock
A shock is a single event of sudden change in acceleration. Normally the shock is defined to be a half sine pulse. That means the shock duration corresponds to half the period and the magnitude to the amplitude of a sinusoidal acceleration. A typical specification for a shock could be: Half sine shock of 5000g / 1ms
Shock resistance
The capability to survive a shock is given by the design and material choice of the accelerometer like we have seen for the upper limit of the dynamic range. Not to forget that a shock survivability requirement is normally meant for all 3 axes!

Shock profile with half sine wave shape
To produce a repeatable shock there are different systems on the market.
One of them is a pneumatic hammer i.e. there is a cylinder with a piston inside which is shot pneumatically to impact a little anvil. On the anvil the transducer under test together with a reference transducer are mounted in one axis similar to the back to back mounting of the sensitivity calibration.
Other methods are the pendulum shock testing machine which works like the name says with an impacting pendulum or the free-fall drop shock machine which has a vertically guided drop table on which the UUT is mounted.
Shock measurement
The correct measurement of a shock with a piezoelectric accelerometer is quite complex and a little tricky. It is not only a question of the amplitude range, but mainly a question of the frequency response of the accelerometer. The piezoelectric accelerometer has virtually no damping and therefore the influence of the resonance excited by the shock must be taken into account. To measure a shock, an accelerometer with the highest possible resonance is needed. But the lower end of the frequency band is also important, as the frequency content of even a very short shock contains very low frequencies. Furthermore, certain piezo materials show a kind of zero shift after a large shock, which only recovers slowly.