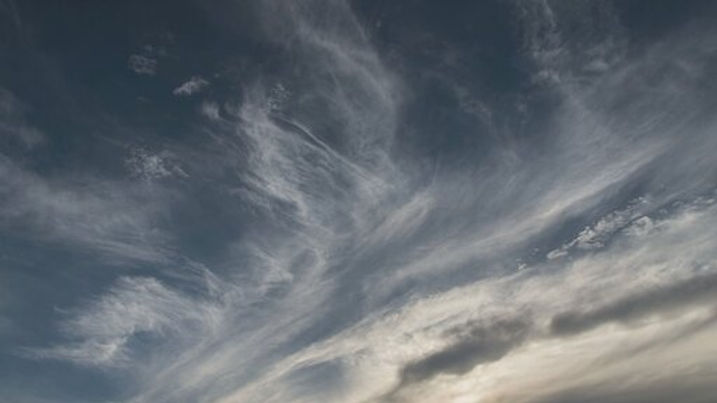

Piezo Accelerometer Tutorial
Accelerometer Design
Electromagnetic Interference
When designing a sensor we also have to consider the electromagnetic environment . The surrounding power lines, electronic devices and other electrical equipment may create so called electromagnetic interference (EMI). The effects of the electromagnetic fields may be picked up by the sensor and particularly by the connecting cable and degrade the weak measuring signal.
The solution to reduce or eliminate these problems is proper shielding and grounding.
The shield
The shield is a metal sheath or braid and must surround all parts of the measuring circuit, the sensing element, the signal conductors and finally the charge amplifier.
It can reflect some of the energy and it can pick up the noise and conduct it to ground so the EMI does not reach the internals. However some of the energy still passes through the shield, but it is highly attenuated.
The shield needs always a solid connection to the ground.
A floating shield (= not connected to the ground) provides no protection against electromagnetic interference.

remaining energy
radiated EMI
reflected energy
inside
outside
shield
energy conducted to ground
The shield will reflect some energy, conduct most of the energy to ground, but also pass some energy.
The accelerometer
On the accelerometer the electrical shielding is provided by the cover and the base part.
In the chapter "Functional Modes" we have seen some different electrical layouts of the sensing element like “single ended" or “insulated”. The choice of such basic design characteristics depends on the system design in which we want to use the accelerometer.
We distinguish two different electrical architectures:

Single ended accelerometer.

Floating design accelerometer.
In the single ended design one pole of the sensing element is connected to the housing while in the insulated design both poles are insulated from the housing. This double-sided insulation is also called electrically floating .
The figures show the electrical diagram of the two basic layouts. The shield (the housing) is shown dashed.
The signal cable
The signal cable is already more difficult to shield. We want the cable to be flexible and therefore the cable shield is mostly braided and has therefore many little holes which reduce the shielding efficiency.
It is important to know that due to the length of conductors extending beyond the shield we may loose a lot of the protection. Ideally the shield is connected over the full circumference.
EMI Effects on the Single Ended measuring circuit
The single ended circuit
The accelerometer, shielded cable and charge amplifier form the complete measuring circuit.
The symbol of an amplifier is a triangle and the dashed box indicates the shield. All components are single ended that means there is only one live pole while the other pole is connected to the shield.

Complete measuring circuit with single ended components: Accelerometer, shielded cable and charge amplifier
charge amplifier
Capacitive Coupling
The electrical shield on a cable is always leaking somewhat. Due to the intimate contact of the shield along the center conductor there is a certain electric capacity. There are also capacities between the shield and any internal component but much smaller. These capacities are indicated in blue.
Because the grounding of the shield is never absolutely perfect some noise is coming through although most of the EMI energy is captured and led to ground.
With increasing cable length the cable capacity is growing and the grounding is getting less efficient. We therefore find this kind of architecture only when relatively short cables may be used.

charge amplifier
Radiated EMI
Radiated EMI builds up a voltage on the shield. Capacitively coupled noise is coming through.
Most of the EMI energy is captured and led to ground
Ground Loop
In an industrial environment, the machine or equipment on which the accelerometer is mounted may show a certain voltage with respect to the ground at the electronics rack. If we now connect the shielding to ground on both sides, a so-called ground loop is created in which a current can flow.
Also in this case noise can be induced due to the cable capacity between the shield and the conductor. This effect will of course get worse with increasing cable length.
A simple counter measurement consists in isolating the accelerometer from the machine so the loop is interrupted.

charge amplifier
Ground loop current induced by different potentials between ground locations. Noise is coupling through due to cable capacity.
Triaxial System
A further improvement can be obtained when we add an additional shield to the accelerometer and
cable. We end up then with a so called triaxial system. The external cable shield is only grounded at one end to avoid any ground loop, while the internal shield still works as signal return.
A triaxial architecture provides excellent protection from EMI.

Triaxial circuit (accelerometer and cable)
charge amplifier
EMI Effects on the Balanced Measuring Circuit
A somewhat different approach to fight off EMI is to use an electrically balanced sensor, cable and charge amplifier. Balanced in this context means that the components are fully insulated from ground and both sides positive and negative are symmetric. That means we have for the positive and negative side two identical conductors and then a shield over both conductors. Like this we obtain identical capacities from both poles to the shield and thereby from both poles to the ground (which is not the case for single ended circuit).
Differential Charge Amplifier
The heart of a balanced circuit besides balanced accelerometer and cable is the use of a so called differential charge amplifier.
In the differential charge amplifier both inputs, positive and negative are treated exactly identically. In contrast to the single ended circuit the negative pole of the piezo element is no longer connected to ground and we find a separate charge amplifier for each line, each with a separate intermediate output voltage V1 and V2.
The third amplifier is called differential amplifier because it produces the difference between two voltages V1 and V2.
It’s output is basically Vout = V1 - V2

charge amplifier 1
charge amplifier 2
differential amplifier
V1
V2
The piezo element has the nice characteristic that it produces a positive charge signal on one side and the same but negative charge signal on the other side. This kind of signal is called differential signal. This is ideal for the differential amplifier as it will invert the signal on the negative side and add it to the signal on the positive side.
On the other hand if same signal or noise is applied to both inputs (so called common voltage) it is rejected in the output because it's difference is zero.
In short: The differential signal is passing while the common mode noise is blocked off. The figures below are showing this.

differential charge amplifier
+ signal
- signal
output
The differential signal is amplified

differential charge amplifier
noise
noise
output
The common noise is cancelled
Besides the amplifier itself all the other components at the input of the differential amplifier must also be balanced. That means the capacities of either pole to the shield of the accelerometer and cable should be equal.
Capacitive Coupling
Here is a complete balanced circuit with the accelerometer, cable and differential charge amplifier. Like in the single ended situation the EMI noise is mostly captured by the shield and led to ground. The two conductors capture also a small part of the noise but due to the balanced circuit the noise on both lines is practically the same and the at the output of the differential amplifier the noise will be largely suppressed.
It is important that the shield of the cable is grounded only at one end!
This is to avoid any ground loop. Normally the quality of the ground is better at the electronics end than at the machine.
That is why this is the preferable end to ground the shield.

differential
charge amplifier
Radiated EMI
Capacitive coupling is symmetric and practically identical on both signal lines. The differential charge amplifier will largely suppress the noise.
Low Noise Cable
Regarding charge transmission cables there is a last but not least consideration. Mechanical displacement of a cable due to vibration or bending can induce electrical charges by friction inside the cable. This is called triboelectric effect and can result in quite significant noise in the measuring signal.
Low noise cables are designed specifically for charge signals of piezoelectric accelerometers.
A special semi-conductive layer between the insulation and the shield reduces this noise considerably.
It is better to avoid the problem than fight the consequences. That means charge carrying cables must be clamped down carefully. They should never flap with vibration nor bend too much.